Okay, so I've ordered the ring gear style timing wheel for my LandRover. Ring Gear because the crank pulley has a starter handle dog in the middle of it and although I've never had to hand start it I'll need to if I loose the ability to (Sod's Law, and all that).
Anyway, I read somewhere on here a comment about using expoxy to fix on a timing wheel rather than welding.
Is this realistic? If so, is something off-the-shelf like Araldite good enough? What surface preparation would be needed?
Or should I just take it to the garage and beg them to be very carefull when they weld it?
Glue or weld?
Moderators: JeffC, rdoherty, stieg, brentp
Absolutely have the ring
Absolutely have the ring welded. If possible, have a groove machined into the ring so the edge of the pulley sits just inside the ring, locking it in place (so to speak).
The forces generated are tremendous, needless to say I experienced my own failure. Not through the use of adhesive, mind you; In my case I bolted the ring to the pulley. Eventually the ring developed a wobble and broke off the crank pulley with tremendous force.
Mounting it correctly is worth the investment in time and money; without this timing wheel installed correctly you will be stuck at the side of the road.
Brent
The forces generated are tremendous, needless to say I experienced my own failure. Not through the use of adhesive, mind you; In my case I bolted the ring to the pulley. Eventually the ring developed a wobble and broke off the crank pulley with tremendous force.
Mounting it correctly is worth the investment in time and money; without this timing wheel installed correctly you will be stuck at the side of the road.
Brent
-
- Posts: 122
- Joined: Tue Jan 10, 2006 8:17 pm
- Location: North Yorkshire, UK
I'm new to the Megajolt system
I'm new to the Megajolt system, but I'm looking to get a 36-1 tooth wheel laser cut to my own design to fit to a modified sierra double front pulley for my Capri. As yet, I havn't really got anywhere with it. I was thinking about bolting it on, but now, I think I'll get the pulley turned down to suit the 36-1 ring at work and weld the ring onto the pully and will probably dowel it too. The one thing that worried me is the possibility of the toothed wheel slipping or coming off at high RPM (my 2.1 pinto revs to over 7K).
sample
Here's an example of what I had done:
<img src="http://picasso.org/misc/mr2/engine/timi ... face.jpg"/>
<img src="http://picasso.org/misc/mr2/engine/timi ... ose2.jpg"/>
<img src="http://picasso.org/misc/mr2/engine/timi ... _end.jpg"/>
<img src="http://picasso.org/misc/mr2/engine/timi ... face.jpg"/>
<img src="http://picasso.org/misc/mr2/engine/timi ... ose2.jpg"/>
<img src="http://picasso.org/misc/mr2/engine/timi ... _end.jpg"/>
Araldite
Dont even consider Araldite. Although in some applications this type of adhesive will cope with the stresses. Araldite & many eproxy based products actually get softer when the get hot. This is the primary problem, as failure inside the adhesive layer would occur due the heat and vibration combined.
Personally my wheel is bolted as I have a convinent set of 4 bolts that hold the pully on that I have utilsed.
Personally my wheel is bolted as I have a convinent set of 4 bolts that hold the pully on that I have utilsed.
Just curious, but did you
Just curious, but did you have the pulley balanced after welding on the tooth ring? How important is balance in these applications? I'm planning on using the stock sensor and 36-1 tooth ring on the back of the fly wheel for my Zetec application but I've been thinking about putting a MJLJ on my 231 Buick powered 46 Willys Jeep just for kicks. If I do I'll have to mount a tooth ring on it. Thanks,
Jack
Jack
Jax2A
Ahhh
Thanks for all of this info. I shall certainly get the wheel welded. I only asked about epoxy 'cause somebody else had mentioned it.
I like the idea of getting the grove turned into the pulley. I'd been wondering how to make certain that it was really in the centre. I'll have to find somewhere round here to do it.
Cheers!
I like the idea of getting the grove turned into the pulley. I'd been wondering how to make certain that it was really in the centre. I'll have to find somewhere round here to do it.
Cheers!
balanced
Balance is important, you can certainly feel the missing tooth when the trigger wheel is spinning 6000+ rpm
My trigger wheels is bolted on the pully with a single center bolt.
I have balanced the the trigger wheel with a 4mm screw, the screw also acts as a fixing point going into a grove I have made in the pully.
The screw obviously sits just under the missing tooth.
I balanced it by fabricating a small aluminium disc that I dropped into the center hole. Then I drilled a 1mm hole in the aluminium and put a needle thru. Placed the wheel on the needle between 2 ring keys, or ball berrings if you are very concerned about balancing.
Then spin the wheel
and watch it settle exacly the same place every time.
I tabed a screw into the top position(the lightest position, just under the missing tooth) and slowly adjusted the length of the screw until the weel stopped at random places when spinning it.
Now make a grove in you puly at 90dgs before VR at TopDeadCenter, bolt your wheel to the pully and screw the balancing screw into the grove in your pully.
I worked for me
/jano
My trigger wheels is bolted on the pully with a single center bolt.
I have balanced the the trigger wheel with a 4mm screw, the screw also acts as a fixing point going into a grove I have made in the pully.
The screw obviously sits just under the missing tooth.
I balanced it by fabricating a small aluminium disc that I dropped into the center hole. Then I drilled a 1mm hole in the aluminium and put a needle thru. Placed the wheel on the needle between 2 ring keys, or ball berrings if you are very concerned about balancing.
Then spin the wheel

I tabed a screw into the top position(the lightest position, just under the missing tooth) and slowly adjusted the length of the screw until the weel stopped at random places when spinning it.
Now make a grove in you puly at 90dgs before VR at TopDeadCenter, bolt your wheel to the pully and screw the balancing screw into the grove in your pully.
I worked for me

/jano
Spandit, yes you can do that but make sure it is really centered well.
I have an aluminum V pulley on my crank. Obviously my 'Jolt pulley is steel/iron center. I machined a sharp-edged lip on the crank pulley and a corresponding one in the 'Jolt pulley. They fit VERY snug, an interference fit almost. Four hardened bolts with nyloc nuts to back them up hold mine together. Almost three years, over 10,000 miles and 6500 rpm shifts and all is still well.
I have an aluminum V pulley on my crank. Obviously my 'Jolt pulley is steel/iron center. I machined a sharp-edged lip on the crank pulley and a corresponding one in the 'Jolt pulley. They fit VERY snug, an interference fit almost. Four hardened bolts with nyloc nuts to back them up hold mine together. Almost three years, over 10,000 miles and 6500 rpm shifts and all is still well.
I first printed out a template of my trigger wheel with hole positions on it then stuck this to the trigger wheel.
I used this to accurately mark and drill 3mm holes in the wheel.
I then glued my trigger wheel to the back of the pulley then, once the Araldite had set, I drilled 3mm holes into the cast iron pulley. These were then all drilled out to 3.2mm (I have plenty of 3mm bits but only one 3.2mm bit) and then tapped to M4. After degreasing, I screwed in 4mm hex-socket screws with threadlock and spring washers
Here's the pulley. For some reason I forgot to take a picture of it with the trigger wheel installed and it's now back on the vehicle:
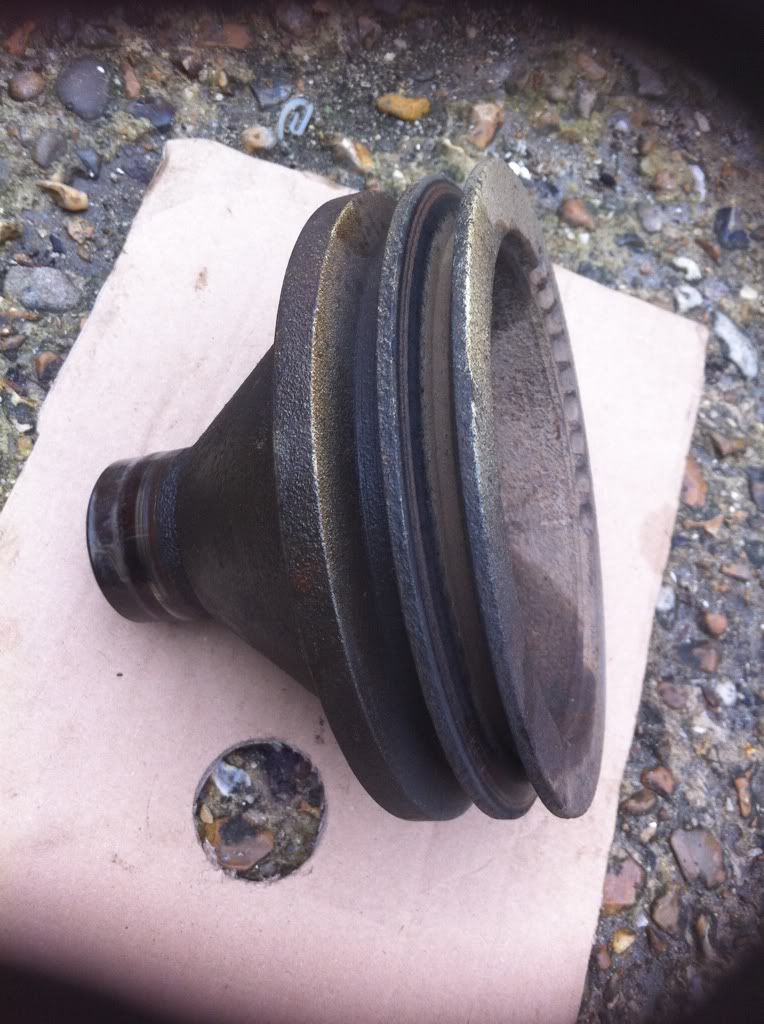
I used this to accurately mark and drill 3mm holes in the wheel.
I then glued my trigger wheel to the back of the pulley then, once the Araldite had set, I drilled 3mm holes into the cast iron pulley. These were then all drilled out to 3.2mm (I have plenty of 3mm bits but only one 3.2mm bit) and then tapped to M4. After degreasing, I screwed in 4mm hex-socket screws with threadlock and spring washers
Here's the pulley. For some reason I forgot to take a picture of it with the trigger wheel installed and it's now back on the vehicle:
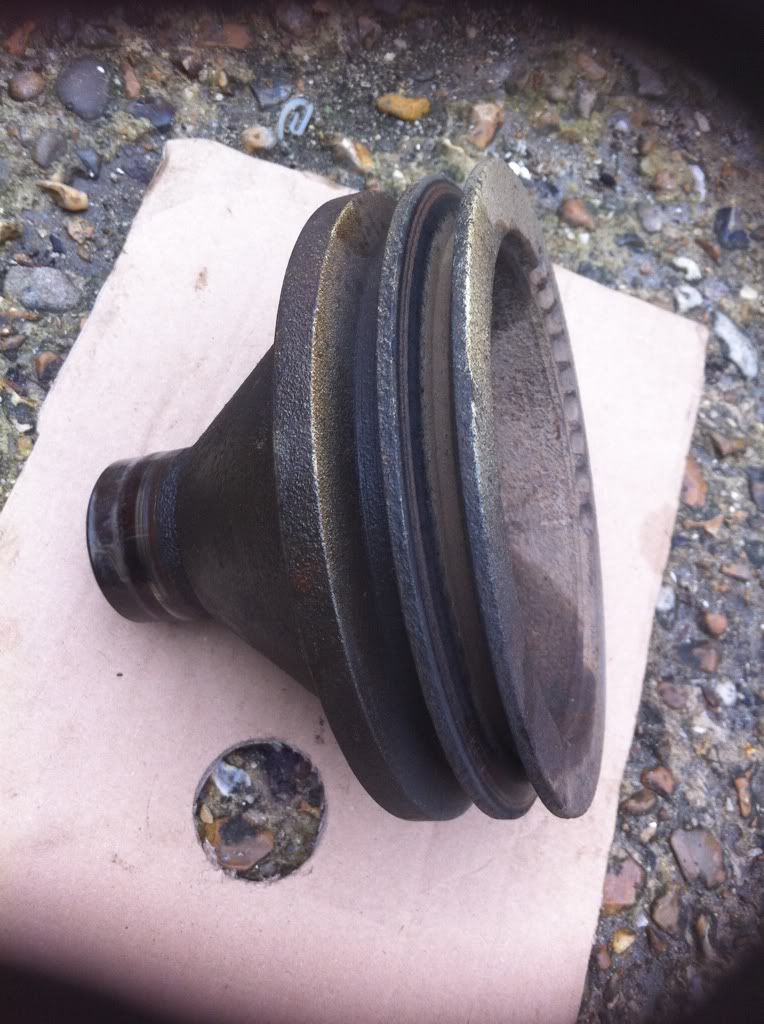
Sorry about replying to my own post...
Because I'd been an idiot and lined things up wrong, I had to take the trigger wheel off the pulley today. Thinking it would be a pig of a job because of the epoxy I'd used... however, one very gentle tap with a chisel and off she came! Good job I had used bolts as well.
Now I've got to redrill the bloody thing and hope I get it in the right place this time...
Because I'd been an idiot and lined things up wrong, I had to take the trigger wheel off the pulley today. Thinking it would be a pig of a job because of the epoxy I'd used... however, one very gentle tap with a chisel and off she came! Good job I had used bolts as well.
Now I've got to redrill the bloody thing and hope I get it in the right place this time...